Teach you to assemble the aircraft carrier
Author:Institute of Physics of the Ch Time:2022.07.07
aircraft carrier--
Floating Maritime Airport
The symbol of national navy equipment and national defense strength
In 2012, Liaoning, the first aircraft carrier in China, officially entered the Chinese Navy with the port number "16".
In 2017, the second aircraft carrier Shandong ship was officially launched in my country. The port number was "17". The construction of domestic aircraft carriers in my country has entered a new chapter.
Shandong Ship Sea "Stall Pancake"
Morning June 17 this year
The third aircraft carrier in my country is named
"The People's Liberation Army Navy Fujian Ship"
The port number "18"
The Fujian ship is the first ejection aircraft carrier that is completely designed and built in my country. It uses a flat and long flight deck, equipped with electromagnetic ejection and blocking device.
The Navy's dream is deep and blue, and it must rely on high -quality equipment. So how does such a huge high -end equipment assembled? Follow the editor of the second middle school to think about it
The first step of raw material preparation
For a aircraft carrier, the basic requirements of metal structures are
Anti -corrosion: The aircraft carrier's combat environment is harsh, the concentration of water vapor is high, and the ability to resist seawater corrosion is required.
High -intensity: It is necessary to withstand a series of loads such as carrier -based aircraft and power systems, so the hull must use high -strength alloy steel.
High toughness: The steel required by the aircraft carrier requires a certain amount of resistance to low temperature and brittleness, as well as strong tolerance to cracks. For example, a dozens of tons of carrier -based aircraft landing on the ship when the ship landed was very high.
………… (and various complex service environment requirements)
The tens of millions of parts of China's first domestic aircraft carrier Shandong ship all adopted domestic products, which realized completely independent design, independent construction and independent supporting facilities
Several typical steels in different parts of aircraft carriers are 1
Steel plates for hulls: In order to prevent torpedo and submarine missiles from attacks, the underwater part of the hull uses a steel plate with a thickness of about 200 mm. Sometimes it will be made into double or three -layer hulls to enhance the anti -strike capacity.
Armored steel plate: Generally use core parts. There are two places on the aircraft carrier. One is the command center with the highest steel plate of up to 330 mm; the other is that the power system of the aircraft carrier should focus on protection. In addition, the bulletproof bolter plates and other places must be protected.
Structural board: It is mainly used for aircraft runways, warehouses and hull structures, etc., which require high strength, large area, and can be used in harsh environments.
For example, the deck as the key part of the aircraft carrier's hull structure. The steel for the deck must not only bear the strong impact of the carrier -based aircraft weighing dozens of tons during the take -off and landing process, but also to bear the tail flames of the jet aircraft. Thousand -degree high -temperature environment. Therefore, the yield intensity of flying deck steel generally reaches 800 MPa (several times the ordinary low -carbon steel), and requires an unevenness to be less than 5 mm/meter, otherwise it will affect the quality of the aircraft lift.
One -third of the construction of the aircraft carrier is welded with steel plates. Therefore, it is necessary to increase the steel plate area of the welding flying deck as much as possible. The fewer subsequent welds are required, and the construction cycle can also be shortened and the overall quality of the deck can be improved.
Because of the high requirements and process conditions, only a few countries around the world can produce steel for decks built by aircraft carriers. The five -meter and five -super wide rolling machine, known as the "King of the World", is assembled in Ansteel Group 2 in my country.
Ansteel Group's five -meter five -super wide rolling machine production line
This ultra -wide rolling machine has top rolling capabilities. The downward rolling system of up to 100,000 tons can roll a steel plate with a width of 5.5 meters. The rolling length can reach more than 40 meters. It is a strong guarantee for the production of aircraft carrier deck.
Step 2 Material Pre -processing
The busy production workshop of the Big Ship Group of China Ship Group 3
Send the metal mother material used in the shipbuilding house to the pre -treatment line, and perform geometric shape correction, sandblasting, rust removal, and painting.
First of all, geometric shape correction to ensure flatness. By heating, the water on the surface of the steel plate can be removed, loose oxidative skin and rust spots, which is convenient for subsequent removal.
Then removing rust: The commonly used rust removal method is shot shot and rust (spray the abrasive at high speed to the surface of the steel plate, and peel the oxide and rust spots) and chemical rust removal (react with the oxide and rust spots with acid liquid) 4.
After the paint paint: workshop primer has good wear resistance and impact characteristics, dry and fast, does not affect the subsequent cutting and welding quality.
Finally dry: The method of drying the paint film is infrared, far infrared and electric heating 4. After the steel plate is dry, the next step is passed after the quality inspection and marked.
Step 3 Component processing
The formation of aircraft carrier materials must not only have a specific shape size, but also meet the performance requirements.
Traditional cold processing can achieve the purpose of processing specific components by cutting the mother material, such as:
Car worker: Mainly use the car knife to cut the rotating workpiece, and cutting the rotating surfaces of different shapes and different shapes of various sizes, and cutting processing on the spiral surface.
Milling: It is mainly processed with various surfaces of the workpiece with milling cutters. It can process various curved surfaces such as planes, grooves, and spiral surfaces.
Plane: Plane, grooves or forming surfaces of the workpiece with a planer.
Moving: Use the grinding gear to grind the surface of the workpiece. Most grinding machines use high -speed rotating wheels for grinding processing.
Driving processing | Picture source network
Milling and processing | Picture source network
Thermal processing can deform the materials under the condition that the volume of the mother material is basically unchanged, such as rolling, molding, squeezing, pulling, and plate stamping, all of which are in the category of heat processing. For example, mold forging is a forging method for forging by using molds to form the blank formation on the dedicated mold forging equipment. The forging size produced by this method is accurate, the processing remaining amount is small, and the complicated structure can be processed.
If you want to achieve large force, working space and long stroke, and long -term pressure preservation, you can choose a hydraulic press
80,000 -ton mold forging pressure machine for Chinese dual companies | Tuyuan Network
If you want to choose the itinerary and stroke position freely, achieve fixed force control, the fixed -course control and energy control, you can choose a spiral pressure machine
Spiral Pressure Machine | Picture Source Network
In short, forging thermal parameters must be comprehensively determined according to equipment, mold shape, mold shape, forging temperature, deformation degree, cooling rate, etc. to create components that meet the requirements.
Step 4 assembly
The focus is here, thinking about a question, and after the basic component, how can we connect them?
Is it used to use Fan Dehua's glue?
How can this be possible?
Think about the rivets on the wing of the aircraft. The connection method mainly connected by the bolt is still not enough for the aircraft carrier, and this connection method is not sealed and easy to enter the water.
So the connection method can only be selected -welding
(Enter the reconstructed metal key through the hot field and the force field)
For welding mainly based on thermal source, the process in which the process is a deep science. There are not only handmade arc welding commonly common on the street, but also sink arc welding (mig), buried arc welding (SAW), tungsten pole arc welding welding welding (Tig), plasma arc welding (PAW) and other advanced arc welding, as well as electronic beam welding and laser welding.
Non -automatic laser welding equipment 5
Laser-Boolis arc welding mixed welding schematic diagram 6
Here is an analysis of a basic melting welding process:
First of all, the welding thermal source is modeling, and the welding thermal input has local concentration characteristics.
In the plate welding, the Gaussian heat source model is a distributed heat source model. It is assumed that in the area covered by the arc on the surface of the workpiece, the distribution of heat flow density can be described by the Gaussian normal distribution function in the probability analysis. Sometimes the welding torch is used into a column of simultaneous heating workpieces. For this situation, it can be described by a band -shaped heat source.
The distribution of thermal density of Gaussian heat and band heat sources 7
For thick plates, the accuracy of the above model calculation is reduced, such as high -energy beam welding thick plates. In response to this situation, a semi -semi -distributed volume heat source that is similar to the shape and size of the welding molten pond is used to describe the deep melting surface pile welding or docking weld, that is, the double ellipse heat source model.
Sports double ellipsoid heat source model with a normal heat flow density 7
The heat source can not only provide the energy required for the molten mother material, but also cause changes in the micro -mechanical properties of the materials around the weld:
When welding the metal component, the mother material will swell after heating, and it will shrink after cooling. The temperature changes will cause it. If this deformation is constrained, it will generate stress inside the transmission tower. This stress is called thermal stress. If the alloy also has structural changes during heating, it also causes the volume of the material to change and cause deformation. If the volume changes brought by this change are restricted, the stress will be generated.
When the welding seam is cooled from high temperature, the volume is shrinking and the stress of the surrounding materials is subject to the stress of the surrounding materials. In order to maintain a stress balance, the edge of the welded parts is affected by the pressure stress.
Distribution of residual stress (vertical stress) in the direction of welding
For tablet docking type, when the weld is relatively long, a stable area will appear in the middle of the weld. Because the end surface of the board is the free boundary, there is no material outside the end surface, and its internal force value is naturally zero.
During the tablet docking, the vertical stress on the weld is distributed along the length of the welded seam 7
For the ring weld on the cylindrical cylindrical, because the degree of freedom of its vertical contraction is larger than the contraction of the tablet, its longitudinal stress is relatively small. The size of its longitudinal residual stress value depends on the width of the radius, wall thickness and plastic deformation zone of the cylindrical.
The distribution of the vertical stress of the cylindrical welding seam 7
Residual stress (horizontal stress) distributed in the direction of welded seams
Due to the horizontal contraction when the weld is cooling, the horizontal stress manifests in the form of pressure on both ends and pulling the middle. When the weld is long, the tensile value of the center part will decrease and gradually approach zero.
Comparison of the horizontal stress on the welding seams at different lengths 7
The direction and order of welding will inevitably affect the horizontal stress. The first welding part cools and restores elasticity, which will cause a hindered effect on the horizontal contraction of the rear cooling part, thus producing horizontal stress.
The impact of different welding directions on horizontal stress distribution 7
The above is only considered the stress distribution of the simple melting welding of the plate. If it is thick plate, restrained state, and changes in the material structure caused by the material structure, there is a more complex analysis.
Under the influence of the temperature field, the crystal structure and orientation of the atomic discharge of the metal material will change to a certain extent with the heating temperature and the cooling rate, which determines the strength and quality of the weld.
Micro structure of materials around the weld: Each area represents a certain atomic discharge method. Different colors represent different orientations of atomic discharge. 8
The optical microscopic image of the welded joints of aluminum lithium alloy T -shaped welded seams, the upper and lower parts are a series of pictures on the top and bottom of the melting area, showing the size and appearance of different areas of different areas affected by the temperature field. If the welding parameters are not controlled well, slight cracks will appear in the weld, which will cause great harm to the subsequent component service process.
Observation of aluminum lithium alloy T -shaped welding area observed by optical microscopes appears in the upper part of the welding and melting area of the welding area.
In macro, if the welding process is not well designed, the residual stress after welding will cause severe component deformation, such as below:
T -type welding angle deformation 7
Wave deformation of the flat panel 7
Donary roundness caused by deformation of the cylindrical welding 7
In the actual welding production process, various welding deformation often appears at the same time, so reasonable design of welding process and stress distribution is very important for the manufacturing of large equipment.
The carrier deck has many different specifications of steel plates to be spliced 11
During the construction of the aircraft carrier, 30%of the working hours consumed are the workload of welding workers. Each welded seam requires an X -ray test, and the flatness of the interface is controlled below 3 ‰.
Each steel plate is not only welded with the name of this steel plate and the welder, but also the weather conditions faced by the welding work on the day, such as temperature and humidity, and even a series of environmental parameters such as wind speed 12
The quality of the weld is very detailed, and behind it is the spirit of many unknown shipbuilders.
In the component assembly welding and segmented assembly welding, it is necessary to fully consider:
The weight and size design of segmented manufacturing: The total weight of the segments does not exceed the lifting transportation capacity of the shipyard. Secondly, the structural rigidity caused by the size of the segments is not enough, that is, it is difficult to control the assembly accuracy.
The rationality of the assembly process: It is necessary to consider the needs of subsequent equipment operations as much as possible, but also expand the range of segmented welding automation and shorten the working hours.
For general aircraft carrier power systems, an independent propulsion device is formed by the connection of the original motivation and the promotional machinery mechanical. The power required by the auxiliary machinery and living systems on the ship is responsible for the supply of the independent shipbuilding power station. In the choice of the original motivation, you can choose a steam turbine/gas turbine/nuclear power.
In terms of overall architecture, the construction method has the construction method of the total section (first transport the base section of the ship to fix the total section of the ship, and then hang the adjacent total section before and after in turn), the tower construction method (at the time of the construction of a certain part of the middle part of the part, a certain part of the middle part The bottom section is the benchmark segment, which is expanded forward and backward, from the bottom up, hanging in turn), two sections of the construction method (divided the hull into two sections, and each is completed in the table or the dock).
What is the future smart ship factory?
Lin Zhongqin, an academician of the Chinese Academy of Engineering, described the vision and implementation path of "smart manufacturing of ships". Entering the era of artificial intelligence, as long as the technicians lighten the mouse in the background and issue various execution instructions, they can control the robot to build ships. At the same time, the on -site operation can be visualized based on the three -dimensional model, and the design information to the site seamless docking and accurate transmission.
The intelligent manufacturing of the ship and the comprehensive automation and intelligence of the manufacturing process can not only liberate people from the operating environment of "bitterness, dirty, tired, and dangerous", but also promote the development of the shipbuilding industry in the economy, efficient, and comfortable direction. Essence
In 2020, the first robotic production line of Jiangnan Shipbuilding, a subsidiary of China Shipbuilding Group, officially launched operation 13, marking a major breakthrough in intelligent manufacturing.
Jiangnan Shipbuilding Horse Smart Workstation is currently the most advanced ship hanging horse production line in the ship industry. For the first time, it has integrated robot vision recognition, intelligent capture, and intelligent welding technology in the ship industry.
The topic of the "Key Technology and Equipment of Large Shipbuilding Multi -segmented Full Welding Binding Robot" by the China Ship Group's July 1st
Step 5 Laing water and test
The launch of the aircraft carrier is generally used in the floating water of the ship, and the water is injected into the ship to build the dock, so that the ship is naturally floating by its own buoyancy.
After completing the construction of the hull, it will also go through a series of dresses to enter the sea test stage 4. The ship installed refers to the installation of all equipment, installations and facilities of the ship outside the hull structure. According to the three majors of the shipping electromechanical, it is divided into three categories: ship installation, machine installation, and electricity.
The purpose of ship trials is to comprehensively assess the construction of the construction of the construction of ships. There are 4 main navigation test items: comprehensive evaluation of host navigation tests, speed testing tests, manipulation tests, anchoring tests, braking efficiency tests, navigation equipment tests, and sound light signal equipment tests.
Last: delivery
The shipping ship is the final stage of the ship's completion. Shipping is a work in accordance with the procedure. Through some transfer procedures, the shipyard hand over the aircraft carrier to the navy.
Wait ~~~
As mentioned earlier, friends who stick the iron blocks with glue
You are not as imagined
There is a magical metal material -in non -crystal alloy, also known as metal glass
At room temperature: It has a higher intensity than ordinary metal materials
Heating and entering over -cold liquid interval: becoming a good deformation ability like viscous fluid
在 徽 铈 铈 铈 铈 铈 铈 铈 铈 15
Because metal glass excellent liquidity in the over -cold fluid phase area, and different species of materials in the cold solution area, the combination of different material interfaces is very dense, which can achieve the connection of heterogeneous materials. Using the unique thermoplasticity of amorphous alloys (also known as metal glass), it is used as a metal glue to prepare composite materials with regulatory performance 16
At present, this technology is still in the laboratory stage. It can only prepare small -sized materials. I look forward to bringing us more surprises in the future metal glass.
Cover Source: PLA Daily
Reference
https://mp.weixin.qq.com/s/dm7myws0iioe80x8c4dlbq
https://mp.weixin.qq.com/s/pzavbzzdfulfulfae5g9hw
https://mp.weixin.qq.com/s/cqfoopqq6a13i2nn8n0stg
https://mp.weixin.qq.com/s/sk6wxuucat76t1ixwxzq8g
Ning J , Zhang L J , Bai Q L , et al. Comparison of the microstructure and mechanical performance of 2A97 Al-Li alloy joints between autogenous and non-autogenous laser welding[J]. Materials and Design, 2017, 120:144-156.
Wang X , Bo L , Li M , et al. Study of local-zone microstructure, strength and fracture toughness of hybrid laser-metal-inert-gas-welded A7N01 aluminum alloy joint[J]. Materials Science and Engineering A, 2017, 688: 114-122.
Fang Hongyuan. Welding Structure [M]. Machinery Industry Press, 2008.
WU, S. C, Hu, et al. On the flaformation of laser hybrid Welded High Zn 7000 Alloys for Next Generation Railway Components. [J]. International Journal of Fatigeue, 2016,91:110
Han B , Chen Y , Tao W , et al. Nano-indentation investigation on the local softening of equiaxed zone in 2060-T8/2099-T83 aluminum-lithium alloys T-joints welded by double-sided laser beam welding[J]. Journal of Alloys Compounds, 2018, 756: 145-162.
Hu y n, wu s c, chen L. Review on failure behaviviViors of Fusion Welded High-Stringth Al Alloys Due to Fine Equiaxed Zone [J]. Engineering Fracture Mechanics, 2019, 208: 45-71.
https://mp.weixin.qq.com/s/eaw3yrhhu8qytq-ych4hzg
https://mp.weixin.qq.com/s/jz5jmuocsvgtfcpww_ziyw
https://mp.weixin.qq.com/s/_ichpwg0brivupjkspoz3w
https://mp.weixin.qq.com/s/aqgl8nrtnc_eo6jc8ceq6w
Zhang b, Wang w h 2007 chin. Sci. Bull. 52 1477 (INCHINESE) (INCHINESE)
Fu j, yang j, wu k, et al. Metallic Glue for designing composite materials with tailorable propers [j]. Materials horizons, 2021, 8 (6). Edit:
- END -
Is the Fujian ship launching the water on the 17th, is it "coincidence"?
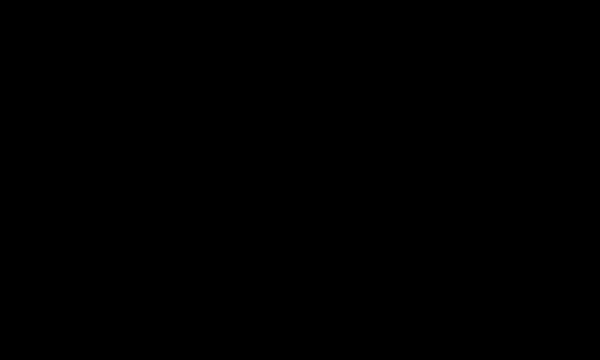
JPEG Webkit-Playsinline On September 17, 1894, the Beiyang Marine Division defea...
The United States and Taiwan's military also linked the Democratic Progressive Party authorities and was willing to be a "grievance"

The United States and Taiwan authorities held high -level military security and th...