Prepare mules, scrape knives, engraving knives ... Make your grandparents' fashion together
Author:knowledge is power Time:2022.06.26
The blue -printed cloth mosquito nets, quilt, baggage, headscarves, tent eaves ... These ancient fashion elements are simple and generous, fresh and bright, and show the beauty of simple and beautiful.
In 2006, the blue printing and dyeing technology was included in the first batch of "National Intangible Cultural Heritage List". Next, let's walk into the blue and white dreams of blue printed cloth together and make the grandparents' fashion together.
Written article / Wu Lingyi (curator of Nantong Blue Printing Flower Museum)
The mystery in dye blue grass
The "Phoenix Opera Peony" blueprints of the Qing Dynasty, Blue Printing Barry Club, Nantong Blue Printing Cloth Museum Collection
The dyes used in blue -printed cloth staining are derived from a class of plants called blue grass. Blue grass refers to the collective name of a variety of plants that can be made of blue dyes and used for dyeing. There are many types, such as: The Blue of the Department of Pupae, the Blue Blue of the Cross Flower, the wood blue of the bean family, and the horse blue of the church family , Roadside green in the Department of Persan.
The "Meizhu Shuangxi" bellyband in the Qing Dynasty, the collection of Nantong Blue Printing Flower Museum
The blue grass is rich in a chemical ingredient called Bluidin (dài). After being soaked in the water in the water, it is soaked and fermented, and the lime powder is added. Stir and contact the air, oxidation to form a blue sediment, that is, obtain a paste -like mud. This mud can be stored for a long time. When dyeing, add rice wine, grass and gray water to the mud, so that the blue blue can be restored into white white, and the dyeing can be performed. As a long history of dye dye dyeing, after witnessing this dyeing change, the Warring States thinker Xunzi sighed "Green, take it in blue, and blue in blue".
In the traditional dyeing workshop, the "watching the cylinder master" is specifically responsible for the deployment of dyeing liquid. The technical key to the dyeing workshop is to prepare the dye solution. The humidity is adjusted in time. If it is not grasped well, the floating color will be serious when the dyed fabric is cleaned, and the color fastness is not good.
The woven blue and white dream
The blue -printed cloth is commonly known as the drug rag. The basic process is to blend the soybean powder and the lime powder into a certain proportion of the anti -dyeing pulp. By the hollow flower version, scrape the pulp into the fabric, and then immerse them into the blue dyeing solution. Because the dye cannot enter the part of the anti -dyeing slurry, a local anti -dyeing is formed, retaining the background color of cotton textiles. After scraping the processes such as anti -dyeing slurry and cleaning, the blue printed flower of the blue flower or blue flower of the blue background is printed and dye. Next, let's take a look at the production steps of the blue printed cloth.
Required tools
Grasson, scraper knife, engraving knife
Tadpole
Scraper
burin
Production step
1. Mount paper
Mounting paper
A paper version of the printed and dyeing blue printed cloth needs to be composed of different paper on 5 to 6 layers. Among them, Guiyang leather paper or mulberry paper 3 layers, 1-2 layers of Gaoli paper, 1 layer of white paper. After cutting these materials into the same size, use the flour paste to mount and compact it to make it a whole. After the drying and solidification of it, cut the four sides neatly, apply a layer of cooked tung oil, dry it to dry, and then dry it. Can be made. Now use cowhide paper instead of traditional handmade paper.
2. Carved version
Stereotype
When operating the paper version of the carving knife, try to ensure that the carving knife is vertically, and strive to consistent with the upper and lower layers. Hold the handle with the right hand, and the middle finger and the index finger of the left hand are holding the cooperation with the pressure. The commonly used carved knife has two types: diagonal mouth and double knife. The single knife is the most important. The double knife is used when the lines that need to be carved with the same width are only used. Round small dots are often made of dumplings made of hammer knocking metal pieces. Under the action of external forces, a hollowed round pattern is formed on the paper version.
Whether it is a soaring phoenix or a dancing male lion, the auspicious pattern of the essence of the blue -printed cloth is exactly the "head corner" under this process. In the design and engraving of the pattern, the iconic cutting knife expression method in the blue -printed cloth pattern is also needed. By separating a long line into multiple short lines, or using the large noodles and lines to interval, this can strengthen the durability of the paper version without destroying the integrity of the pattern. The leakage phenomenon appears. After the pattern engraving is completed, it is also necessary to polish the surface of the paper version with smooth pebbles.
3. Mixing and scraping
Mix
Scrape
After the hollow paper version is made, it can be used for scraping. First of all, we must use soy flour, lime powder and water. Among them, the ratio of soybean flour to lime powder is 1: 0.7, add water to a uniform paste. Soya flour is sticky, can stick to the cloth surface well, and lime powder has a solid and waterproof effect. The cooperation between the two can form a anti -dye pattern area on the cloth surface. When scraping, laying the cloth, put the paper version on the cloth surface, hold the template with one hand, hold the scraper knife in one hand, use a flat mouth scraper to take an appropriate amount to prevent the dyeing pulp, the flat scraper and the layout are tilted at about 45 degrees to quickly scrape and quickly scrape it. Under the bottom, it usually scrapes 3 times from top to bottom, and it should be evenly strong. Strive to put the slurry on average on the flower type, and finally collect the pulp to leave a thin layer of pulp on the surface. After the slurry is completed, the paper version is lifted from the corner of the paper version, and then scraped the next version.
4. Dyeing
dyeing
The scraped cloth needs to be dry naturally in a cool place. When the nails are printed with nails, when the slurry surface is used, it indicates that the slurry can be dyed. Before dyeing, soak the scrape to so that the color is evenly color.
After the blue grass is made, the lime and wine are added to the blue dyeing solution. When dyeing, every 20 minutes, the fabric should be picked out of the dye tank. The dyeing solution is in contact with oxygen, which will produce oxidative reactions, so that the color of the fabric becomes green from yellow to green.
5. dry
Dry
After dyeing, pick out the cloth, drain it on the dye tank, and then use it to dry it out of the sun rack. 6. Scrape
Scrape
The dry dyeing cloth is stacked at randomly with a wooden stick, the mortar on the top is stretched, and then the cloth is stretched on the bracket. One end of the cloth is fixed first, and the other end is tightened as much as possible.
Finally, after cleaning, fixing and drying, the blue printing cloth that condenses the wisdom of folk wisdom was completed.
Inheritance
Wu Yuanxin and his mother Guan Huifang discuss weaving skills
From the end of the Southern Song Dynasty to the late Qing Dynasty, the blue -seated pattern pattern has continued to change with people's life needs and aesthetic taste, which conforms to the needs of people's material and spiritual life. From the late Qing Dynasty to the beginning of the Republic of China, with the introduction of foreign gauze, ocean cloth, and foreign dyes, the blue printing cloth and color printed cloth coexisted, supplemented by each other. Later, due to the prevalence of machine printing, the blue printing cloth gradually faded out of people's lives. However, the blue -seal cloth shows people's pursuit of a better life. It has obtained the aesthetic identity of private collectives. It is one of the iconic visual symbols of traditional culture and an important heritage of Chinese agricultural civilization.
My father, Wu Yuanxin, is a national non -genetic inheritor in the blue print. Under his influence, I have lived in the "Blue and White World" since I was a child. After graduating from the Chinese Academy of Arts, in the face of the dilemma of inheriting the blue and yellow inheritance of the blue -printed cloth, I gave up the opportunity to work in Beijing. I returned to my hometown to take on the burden of inheritance, and inherited the traditional skills of the blue printing cloth to the next generation. So far, we have protected more than 56,000 types of traditional printing and dyeing objects such as blue printing and dyeing and dyeing in the folk, and more than 100,000 patterns, and the blue -print pattern database was established; "Folk Printing and Dyeing Skills", and undertaken the key topic of the National Social Science Foundation Arts "Research on Chinese Blue Printing Flower Facilities".
Today, we have cultivated the blue -printed cloth inheritance in the social, colleges and dyes, and also taught the blue -printed cloth skills in various primary and secondary schools. I hope to sow the seeds of the intangible cultural heritage of China to the children's hearts and let it be let go. One generation cherishes the culture of our country, spreads our culture, and cultivates more blue printing inheritors.
This article comes from the magazine of "Knowledge is Power". The original title "Blue Blue Labor of Blue Blue Flowers", author Wu Lingyi, deleted modification, please indicate the source for reprinting
- END -
The National Reading Classic "Three Hundred Tang Poems" ushered in a short video version, Ye Jiaying led the explanation
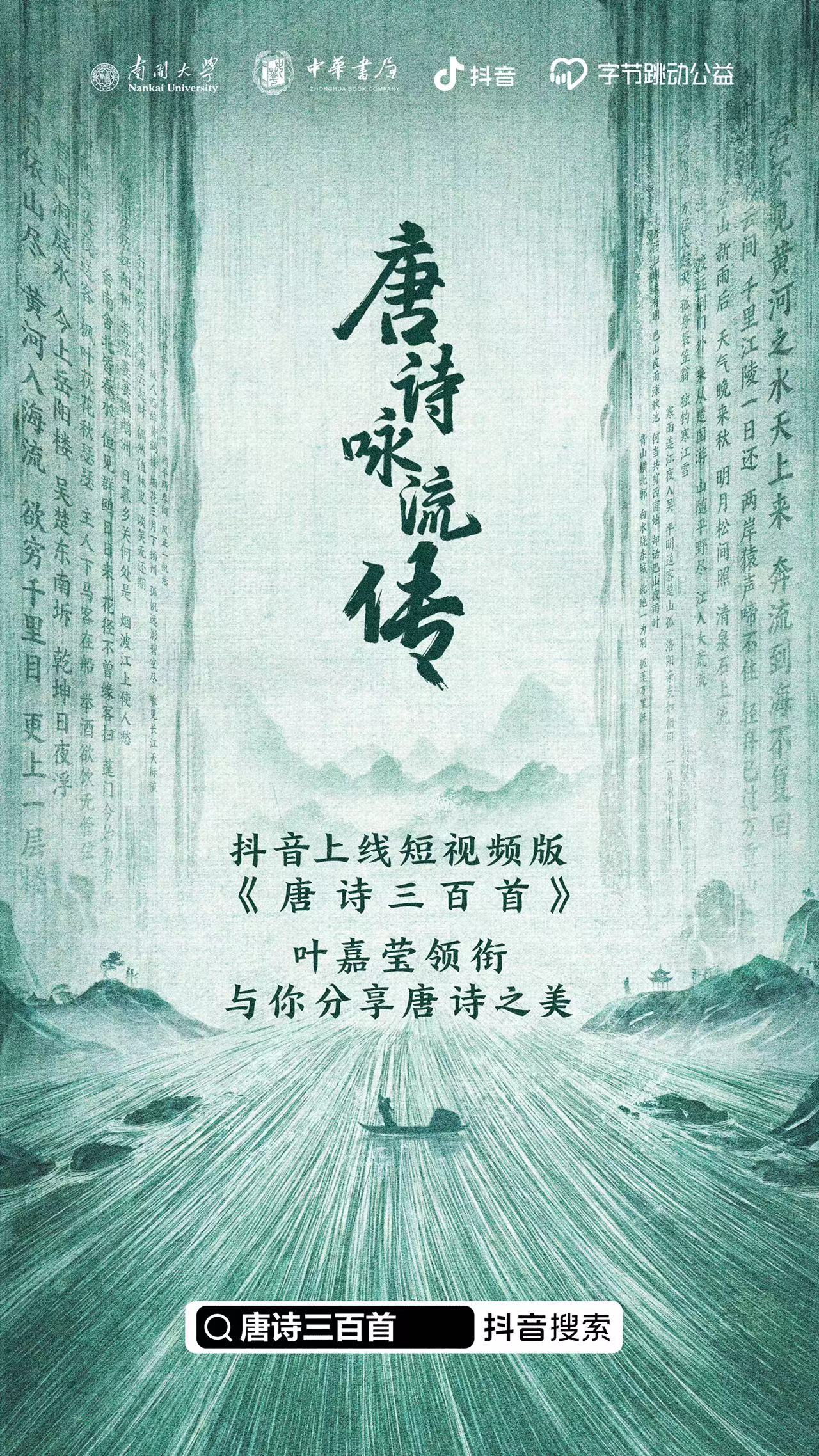
On June 22, the short video version of Three Hundred Tang Poems was officially lau...
Zhaojiaan, Hezhuangping, Hezhuang Ping, Yuanju Pagoda District

In June, Yan Fang had no summer, who knew that there was cool in the world.The hig...