What kind of refractory material should be used for hydrogen metallurgical?
Author:China Metallurgical News Agenc Time:2022.07.06
As we all know, the traditional blast furnace ironmaking is the heat required to react reactions through coke combustion and generate a reducing agent CO, so that the iron ore is restored to iron and generates a large amount of CO2, which is easy to pollute the environment. The hydrogen energy metallurgical uses hydrogen to replace CO to repay the programs. The restore product is water, without CO2 emissions. Therefore, the hydrogen iron purification process is green without pollution.
Metallurgical production is inseparable from the support of refractory materials. The refractory materials related to the long process of steelmaking and short -process arc furnace steelmaking technology have been put into use. The fire -resistant material related to hydrogen energy metallurgy technology is still in the research and development stage. Although the temperature of the iron ore with hydrogen energy is not high (600 ° C to 700 ° C), the restoring effect of hydrogen, especially the flame radiation load of hydrogen plasma, has a high heat load effect of hydrogen plasma. The destruction of the furnace should not be ignored, and it must be attracted to the fire -resistant material workers.
In the context of carbon neutralization, the steel industry's smelting technology is converted from long processes to shortflows, and with the maturity and application of hydrogen energy smelting technologies, it will inevitably promote the growth of new green refractory materials that are adapted.
At present, mainstream hydrogen -making methods on the market: electrolyte hydrogen, hydrogen -made hydrogen, oil -lobed synthetic gas and natural gas hydrogen, nuclear energy hydrogen -making, etc.
(Pictures from the Internet)
Progress -related progress of hydrogen metallurgy and refractory materials
The temperature of hydrogen metallurgy is not high. The hydrogen and iron oxide reactions are generally about 600 ° C. The iron oxide purchased by the laboratory is restored only above 700 ° C. Reacting the reaction process: The hydrogen is decomposed by the water, and then the iron oxide is restored to iron.
The fire -resistant material in contact with hydrogen needs to be valued. It is reported that when the AL2O3/SIO2 ratio of different refractory materials, heated 192h at 1500 ° C in the pure hydrogen atmosphere, the characteristics of the quality loss of refractory materials is that the loss increases with the increase in temperature and the extension of the exposure time in the atmosphere. At high temperature, the material with a high material with high AL2O3 content is less than the quality loss of materials with high SIO2 content.
Among the refractory materials of aluminate, hydrogen energy restores NA2O, TIO2, MGO, SIO2 and other oxides. Hydrogen can make Mo Lai Shi decompose, forming rigid jade and SIO. In the hydrogen material, high aluminum products containing Al2O3 ≥ 85%and Gangyu products are stable. When silicon products are neutral and at 1200 ° C, since SiO2 is quickly reacted, when SiO2 is existed in refractory materials, SiO2 and hydrogen reactions generate gaseous SIO and water vapor. It overflows from refractory materials. SIO2 can also be as good as the refractory material. The water vapor reacts to generate gaseous oxides and is separated from the original refractory material. These two reactions are easy to occur at high temperatures, which affects the service life of refractory materials. Therefore, under the conditions of hydrogen and water vapor, it is essential to strictly control and reduce the SiO2 content of the inner lining refractory material. The fire -resistant materials with high FEO and TIO2 content should not be used under the conditions of restoring atmosphere. For example, the alumina air -hearted brick in the hydrogen protection furnace is better; in the atmosphere of 100%of the hydrogen content, the heat -resistant fiber thermal guidance rate is 2 times larger than in the air.
Refractory material for hydrogen smelting of blast furnaces
Due to the limited hydrogen sprayed in the blast furnace, the role of coke cannot be lost. Therefore, the use of carbon bricks and carbide bricks used in key parts is still very good. In recent years, the non -blast furnace ironmaking process has been vigorously developed. The sponge iron of non -blast furnaces is a good alternative to scrap steel, and the non -blast furnace iron refining equipment is used to refine the equipment.
Directly restore iron refractory material for iron refining
The restore medium has coal, natural gas and gas, etc. The reaction temperature is generally 800 ° C to 1300 ° C. At present, the output of the vertical furnace iron iron with natural gas as the restore medium accounts for about 80%. Because the reaction temperature is not high, the refractory material of aluminum silicate can meet the requirements. The existence of Fe3C will promote charcoal deposition, resulting in brittle cracking of refractory materials. In order to extend the service life, the FE2O3 content should be reduced, the tissue structure is dense, and the pores should be fine.
Found refractory material for melting and restoring iron refining
The melting and restore ironmaking process is to restore the iron oxide under high temperature melting state, and separate the scum iron to obtain carbon -containing iron produced by a blast furnace. Nowadays, more than 30 melting reduction processes have been released, but the Corex method is currently the only process for industrial production. Its advantages are that the consumption of tons of iron is reduced by more than 20%, and the iron -machine pollution decreases by 70%. For the problem of refractory materials for the Corex method of melting and iron, some people use Corex melting restore furnace scum (33.5%CAO, 32.0%SIO2, 20.0%MGO, 14.0%Al2O3, 0.5%Feo) and SIALON (22.08%). ) The anti -residue test of the fire resistance material is that SIALON combines SIC refractory materials in Corex slag. It is a chemical reaction control mechanism, so it indicates that the SIC combination of SIC refractory material has a good resistance to the erosion of Corex slag. Researchers also found that MGO and Al2O3 are the main raw materials. By adding an appropriate amount of Mgalon powder and graphite, and antioxidants, the produced Al2O3 -MGO -MGALON -C quality resistance material W (C) <10%has a good anti -slag. The resistance and thermal shock properties can be used in the melting to restore the refractory material in the furnace, which can obtain a long life.
Hismelt melting and restoring iron refractory materials This ironmaking process can directly use powder ore and non -coking coal to produce iron water. Compared with the blast furnace, sintering, ball groups and coking plants are used. The emissions of CO2 and two evils have small pollution to the environment, but the FEO content in the residue is 3%to 5%, which is 10 times that of high furnaces, resulting in an increased lining erosion and higher iron content S. The effect of chromium-jauding jade bricks CR-10 and CR-50 is better. The use of the dregs line water-cooled box is significantly prolonged. However, because chromium -containing refractory materials are prone to toxic hexavalent chromium, the chromium -free refractory material is the development direction. It is recommended to use the AL2O3-MGO-resistant refractory pouring of the Mgalon, which can significantly improve the erosion capacity of the high-oxygen content zealum residue. The furnace can also be combined with SIALON combination of Gang Jade Brick, SIALON binding carbonized silicon bricks, microneed charcoal bricks, etc.
Hydrogen plasma melting restore iron refractory material for iron refining
Because the hydrogen plasma is much higher than the high -reduction potential of the hydrogen, all metal oxides can be restored to metal, and have the advantages of low emissions, simple process, and small slag. However, this technology has a problem of large erosion of the furnace wall radiation (no foam residue process), and the slag has a large erosion of refractory material. Therefore, the refractory material in the container is one of the core areas of research and development. On the one hand, due to the chemical erosion of the high fever load generated by the plasma flame radiation and the high FeO content furnace slag, the oxide in the refractory material is reduced by excess hydrogen; on the other hand, because some hydrogen will be accompanied by water vapor overflow, hydrogen fails to not all be entirely possible Used to restore iron ore. According to the research results of a University of Mining, Austria, the foam residue generated by the underlying system into the gas through the bottom blowing system can protect the inner lining of refractory materials and avoid high heat shocks. Essence
Conclusion
In the context of the "double carbon", hydride metallurgy technology has attracted the attention of the steel industry at home and abroad. There are many types of hydrogen -making methods, but the cost of greening pure hydrogen by water is high, especially the expensive price of hydrogen plasma is expensive, making many steel companies look forward to it. Therefore, the current hydrogen metallurgical process in my country mainly includes two types of hydrogen wealth and directly returned iron: the amount of carbon reduction reduction of hydrogen wealth of blast furnaces is 10%to 20%, and the effect is limited; and the direct -reduced air -based vertical furnace process can be from the source. Controlling carbon emissions on the top, more than 50%of the carbon reduction reduction of hydrogen riches in the blast furnace, is an effective way to quickly expand directly to the original iron production. Before obtaining large -scale and low -cost hydrogen, it is appropriate to use natural gas, coking furnace gas, and other hydrogen -containing industrial gases.
(Pictures from the Internet)
In the case of less research on hydrical metallurgy, it is inferred that only some basic theories and related data are speculated that hydrogen as an iron ore reducing agent, during the reducing ironmaking process Na2O, TiO2, MGO, SIO2 and other oxides, which make Mo Lai Shi decompose, forming rigid jade and gaseous SIO. In the hydrogen material, high aluminum products containing Al2O3 ≥ 85%and Gangyu products are stable. The fire -resistant material containing Feo and TIO2 is not suitable for use under reduction conditions. Therefore, the hydrogen wealth of the blast furnace uses charcoal bricks or carbonized silicon bricks in key parts of the lining. It is not different from the blast furnace that is completely used to use coke. It is still very good; Low, dense structured silicate refractory material; the Corex method of melting and restoring ironmaking can be used with silicon carbide refractory materials combined with SIALON, or using Al2O3-MGO-Mgalon-C refractory resistance; -10 chromium ductive jade and CR-50 chromium rigida refractory material. In order to avoid toxic hexavalent chromium, it is recommended to use the AL2O3-MGO refractory pouring of the Mgalon. The residue line is used in a water-cooled tank, SIALON combined with Gang jade bricks and carbonized tiles; The system injects the gas and produces foam residue to protect the refractory material. Its lining can consider using carbon and carbide silicon refractory material.
Author | Xu Pingkun
- END -
Zaoyang: Innovative management and protection of farmland water conservancy projects to consolidate the foundation of food production
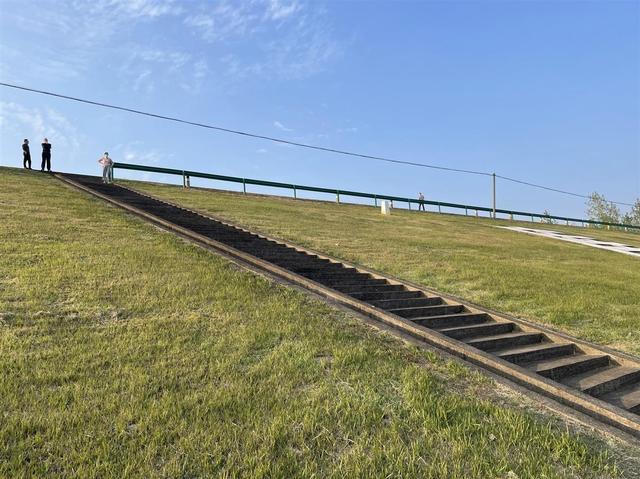
More receivables lies in fertilizer, no harvest is water. The reporter learned fro...
Performance growth accelerates the stock price upward, but important shareholders of Jinye molybdenum shares are determined to reduce their holdings
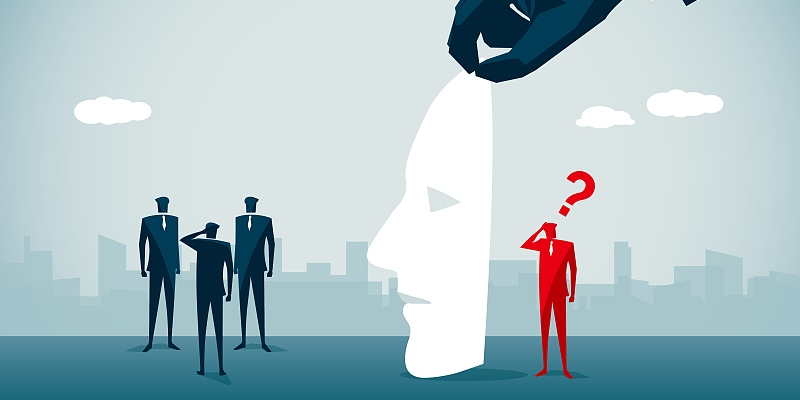
Golden Molybdenum (601958) is one of the few domestic companies with molybdenum -b...